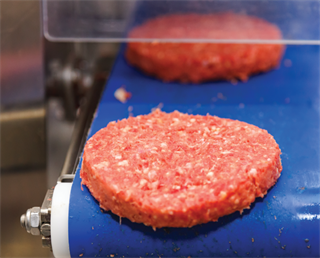
Industry
Food Processing
Application
Endless Belt Splicing for Beef Processing
Product
Novitool® Amigo™ Splice Press 1000
Novitool® Amigo™ Splice Press 625
Objective
- Reduce downtime
- Reduce maintenance time
- Reduce service costs
Conveyor Detail
2-Ply White Food Grade PVC Conveyor Belt
Problem
A large protein processing company with facilities throughout the United States was experiencing various challenges when splicing homogeneous (monolithic) belts. The high level of operator skill needed to complete a splice with wand style tools was causing low splice quality and performance inconsistency. Overall, their splice time was lengthy, and the hour and a half that it took from start to finish was proving to be costly. Additionally, operator safety was increasingly becoming an issue, as their process of squaring belt edges with a utility knife led to lacerations, and the exposed heat wand they were using was causing serious burns to operators. In turn, some of the company’s facilities were contracting third-party splicing services, which created costly downtime from scheduling conflicts.
Solution
The company knew it was time to make a change, so they held a meeting with a key industrial distributor. Once on site and acutely aware of their specific pain points, they introduced Flexco’s Novitool® Amigo™ Splice Press 1000 and 625 to their corporate engineers. There was a keen interest in the products, especially in their splice process steps. By utilizing the Amigo splice press, they knew members of their maintenance crews could easily follow the process to achieve a quality splice every time, all in 20 minutes. And, by splicing in-house, their facilities could schedule maintenance when it is most convenient for them, freeing up their maintenance teams to tackle other projects. Furthermore, the Amigo’s integrated belt cutter and contactless heat emitter took utility knives and heat wands out of the hands of the maintenance crews, which helped to promote a much safer work environment.
Result
After a virtual meeting between the company’s national engineers and Flexco’s Food Processing Industry Manager, along with on-site product demonstrations with Flexco’s local Territory Managers, several sites were ready to make the switch to the Amigo splice press. By implementing the Amigo into multiple facilities’ belt splicing processes, they have seen huge benefits. Not only have they experienced increased belt life from higher quality splices, but the drastic reduction of belt repair time through in-house scheduling has allowed them to reduce plant downtime, increase productivity, and improve profitability. During a follow up on the Amigo’s performance with a key member of their belt maintenance team, they noted that the Amigo’s preheat function to dry moisture from the belt edges prior to the splice has reduced the likelihood of pinholes in the splice, which has reduced the worry of potentially harboring bacteria. This is an especially valuable feature in the world of food processing. In short, the Amigo splice press has allowed this operation to create consistent, high-performance splices, all while being financially viable.