Partner with the EXPERTS in Belt Conveyor Solutions
Please wait while we gather your results.
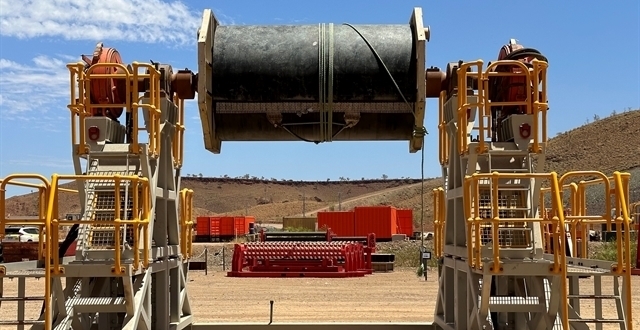
Get Steel Cord Belts From Downtime to Uptime Quicker Than Ever
Flexco knows downtime on steel cord belts drains crucial operation time and eats into the bottom line of many heavy-duty operations. Instead of suffering through downtime waiting for a vulcanized splice to be scheduled, the patented new FXC™ Steel Cord Belt Fastening System can be installed immediately as an emergency splice to get customer belts back up and running or can be used to pull a new belt onto the conveyor system.
LEARN MORE

New MSHA Silica Rules
Flexco takes a look at some of the key changes in RCS monitoring and shares how we can help you combat dust in the load zone with our belt conveyor product solutions.
Learn More
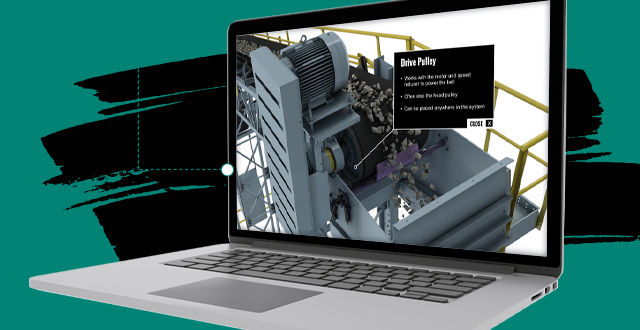
Flexco Essentials™ eLearning is Now Available
High employee turnover? New workers with no conveyor experience? With years of hands-on expertise, let the Flexco experts train your team on the essential components of heavy-duty conveyor systems. Real-world focused content combines with unique, one-of-a-kind learning methods, expert insights, and best practices to focus on pure conveyor training. No marketing, no sales, just the Essentials. Because investment in the next generation of workers has never been more Essential to your operation.
LEARN MORE AND REGISTER TODAY
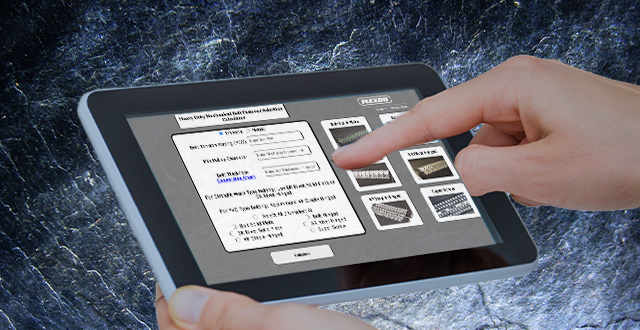
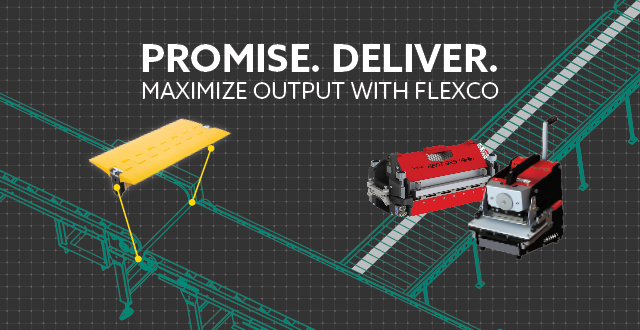
Punching and Splicing of Belts That Drive Live Rollers
The Novitool® Pun M™ NDX Mobile Finger Punch and Aero® 325 Splice Press are the newest timesavers in the Flexco offering of belt splicing solutions. When used together, they ensure the preparation and splicing of the aramid cord belting and traditional thermoplastic belting used in your live roller belt and transport tote application is done right – in a timely fashion.
Read our blog
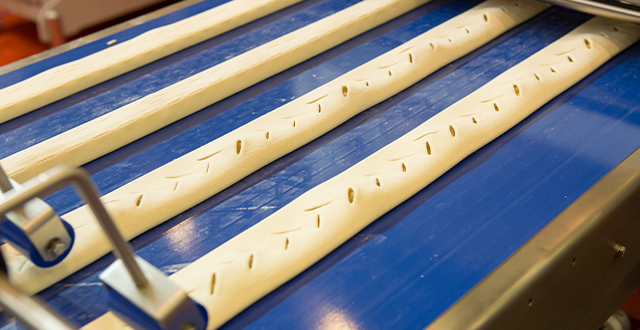
Solutions for Industrial Bakeries
Flexco understands the challenges that operations in the industrial baking industry face. Whether it’s downtime or product loss, we have you covered with solutions that increase uptime, efficiency, and throughput. Find out how one industrial bakery increased their production by $22,000 with the right belt cleaner.
Read More Here
Please wait while we gather your results.
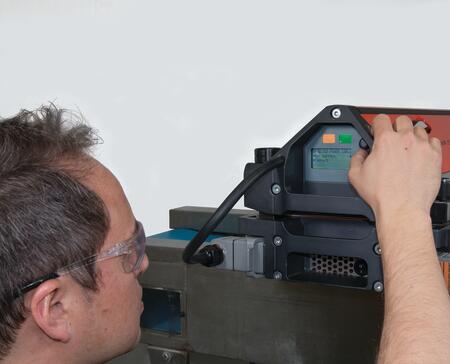
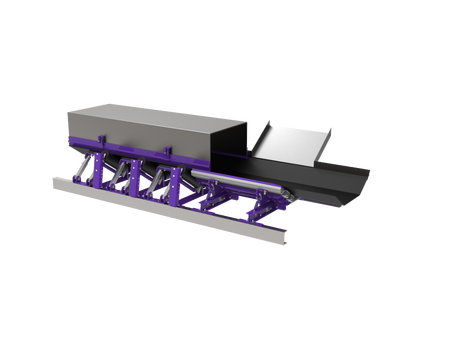
How Ignoring Conveyor Belt Sag Hurts Profit Margins in Mining Operations
February 19, 2025
Belt sag might seem like a minor issue, but in heavy-duty mining operations, its impact can be massive. From increased dust and material spillage to costly belt and conveyor system damage, leaving sag unaddressed eats into profit margins and compromises worker safety. Discover why proactive solutions like the Flexco Belt Support Bar are the key to reducing downtime, enhancing productivity, and safeguarding your operation’s bottom line.
Read More...
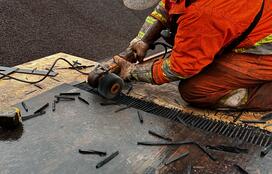
Heavy-Duty Spotlight: Important Questions for Steel Cord Belt Systems
February 04, 2025
Steel cord conveyor belts are a critical component in the heavy-duty mining industry, offering unparalleled strength and performance. But when these belts experience damage, the resulting downtime can be costly and disruptive. Our latest blog explores the key benefits of steel cord belts, the challenges of splicing them, and the essential questions every maintenance team should ask to prepare for unexpected downtime.
Read More...
Please wait while we gather your results.
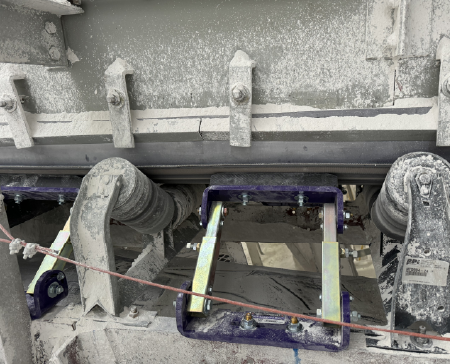
Belt Support Bars Eliminate Costly Spillage for Southeast Nevada Mining Operation
A Southeast Nevada aggregate mining operation was losing valuable material and spending excessive time on cleanup due to persistent belt spillage issues. Their vacuum truck operator was working 8-hour shifts every other day just to clean up scattered debris, creating safety hazards and draining profits. After consulting with their Flexco territory manager, they discovered the root cause and implemented a simple solution. Read how Belt Support Bars transformed their most problematic spillage zone into a clean, efficient operation, delivering immediate results and cost savings of nearly $23,000 annually!
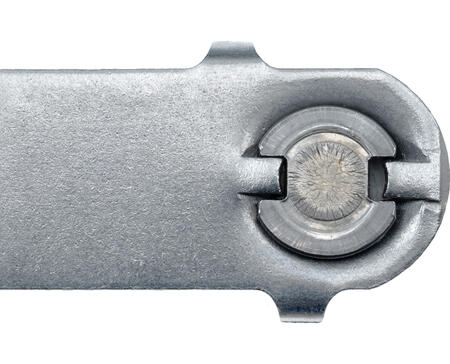
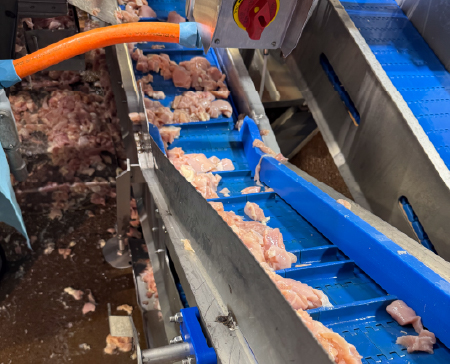
Leading Poultry Processor Cuts Labor Costs and Maximizes Product Recovery with FGP-C
A poultry processing facility in the southern U.S. was spending extra labor hours every day recovering product from the catch pans beneath their trim collection conveyor. After recognizing the rising costs, they reached out to their local Flexco representative for help. Read how the FGP-C Food Grade Primary Cleaner helped them reduce manual cleanup and improve product recovery, resulting in potential savings of over $58,000 per year!