Let’s start with the fundamentals … what is spillage?
Spillage occurs when material falls off the belt conveyor in areas other than the discharge point, usually near the load zone. Across all industries, any material that spills off the belt instantly loses value - costing your operation productivity, maintenance time, equipment life and employee safety. Losing as little as 1% of the conveyed product will increase your operational costs.
Common causes of belt conveyor spillage could be an improperly tensioned belt, inadequate sealing at the load zone, overloading, mistracking, product surge, and poorly-maintained load zone components. Consequently, spillage can become part of a continuous and vicious cycle; mistracking causes spillage, and spillage causes mistracking, which then changes the belt friction, causing the belt to be misaligned, which accelerates component wear.
So, what does this have to do with your load zone?
Spillage can be prevented by properly maintaining your load zone components and keeping the loaded material centered.
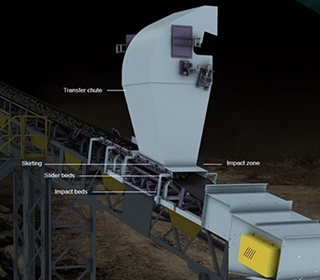
Click to see enlarged diagram.
The load zone is often one of the most overlooked areas for system efficiency, yet it sees every ton of material you are moving in your operation. With the right load point support, you will see improvements in spillage, belt wear, dust emissions, and mistracking, as well as less damage to other conveyor system components. So now that you know the problems associated with load zone neglect, here are a few tips on how to control conveyor belt spillage - these simple changes to your load zone will increase the efficiency of your entire system and decrease the amount of time and money you spend on maintenance!
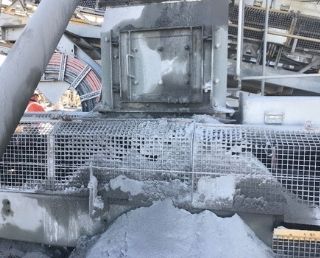 |
Severe skirt damage and spillage issues. |
Tip 1: Seal the load point with skirting systems to eliminate dust
To make operations cleaner and safer, you must seal the load point to control fugitive dust and conveyed material excess. Dust is an important issue many industries deal with, not only because of the major risks that arise for workers who are exposed to breathing in dust or other finely-powdered material, but also because dust is essentially wasted product and significant time may be spent on cleaning up and maintaining damaged equipment.
Skirting systems create an effective seal at the load point without damaging the top cover of the belt, discouraging spillage and dust release.
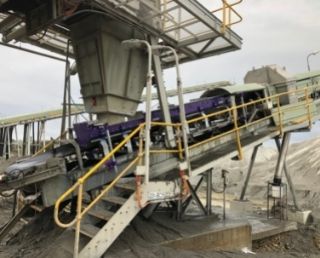 |
Installed 13-metre Flexco enclosed skirting system. |
There are many different belt conveyor skirting systems to choose from that are versatile and easy to maintain. It is important to note that before selecting a skirting system, it is pivotal to consider your application type and productivity goals. For example, in extremely dusty environments, an Enclosed Skirting Systemwould be the most effective solution to contain the airborne particles. Whereas, Standard Polyurethane Skirting can be an effective solution for environments looking to mitigate material spillage. Skirting systems can be easily custom engineered to fit your job requirements, enabling you to protect as little or as much of the conveyor as you need. In saying this, a quarry in Australia defeated dust for good by installing a 13-metre Flexco Enclosed Skirting System.
Tip 2: Add a skirt clamp mechanism to make load zone maintenance easier
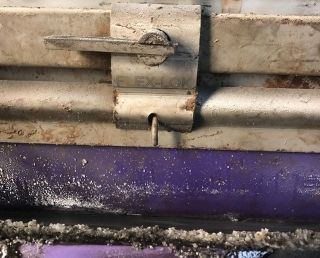 |
Installed Flex-Lok™ Skirt Clamp. |
Skirt clamps allow for efficient replacement of skirting in the load zone, making maintenance easier and safer for repair crews because of the ease of locking and releasing the skirting system. The clamping mechanism should be both durable and provide a stronghold that discourages vibration and drag on the skirt rubber. It should also be easy to service the skirt clamp by providing a simple release mechanism on the clamp, like this one. A simple process to loosen the clamp allows for quick adjustment when the skirting material wears or skirting needs to be replaced. If the process is more complicated than this, maintenance may take too long, or it may not be done at all.
Tip 3: Protect the conveyor belt by preparing for impact with impact beds
Located underneath the belt in the load zone, impact/slider beds offer conveyor belt protection and material containment by controlling acceleration, deadening impact energy, reducing damaging vibrations, and extending belt life. An impact bed can be the solution to these challenges, but first, you’ll need to make sure you have all your specifications correct. You must identify the largest material lump weight and drop height to ensure it can handle the toughest conditions of your application. A simple and informative impact bed calculator can help you choose the appropriate solution for your application.
Impact beds can be used together, along with skirting systems, for a complete load-zone solution. Many beds feature universal components that result in an effective, yet affordable, solution. Flexco DRX™ Impact Beds are designed with one simple goal: to protect the belt. This goal is met by engineering superior belt protection into the entire structure (not just the bars) with Velocity Reduction Technology™. The beds can separate in the middle, allowing the two sides to slide apart and out. This Slide-Out Service™ provides direct access to all the bars and bolts for quick, easy, and safe maintenance.
Tip 4: Get your load zone assessed by an expert
Having load zone components like skirting systems and impact beds will minimize adverse effects across your entire system. These components need to be installed correctly according to your application and maintained properly to see great results in your belt conveyor productivity. To help you see these improvements on your site, you can register for a free on-site load zone assessment. A holistic assessment with a Flexco specialist is not only a simple way for you to generate new ideas for increasing the productivity of your system, but it’s also at no cost to you!
Authored by: Kevin Fales, Product Manager
In the role of Product Manager, Fales manages the Belt Conveyor Product line, providing strategic guidance for the global business unit. This includes identifying product development opportunities and working with global engineering resources to create new product concepts and enhance existing products that meet local market requirements. Fales has been with Flexco since 2010, beginning his time as a Marketing Specialist before moving into the Product Manager position. He graduated from Grand Valley State University with a bachelor’s degree in Marketing, and from Western Michigan University with a Master of Business Administration.