We are currently sitting in the thick of summer and you may actually have a bit of time to take a breath. During this time of temporary respite, I would like to ask you one question: when was the last time you looked under the hood of your conveyor system?
If you can’t answer that, I think it might be time to take ‘er in for a tune up!
Now, I know it’s not the most exciting thing to think about but being proactive in maintaining your conveyor system is arguably one of the best things that you can do for your business. Packages flow and customers are happy; what more could you ask for?
Many of my industry contacts are dealing with similar problems at key points throughout their systems. So, I would like to shed some light on three of the most mentioned areas of concern that others have experienced in an effort to help you with any current or future obstacles.
Tackle the Transfer
No matter which industry you are working in, the belt conveyor transfer point is a major area of concern. Time and time again, packages become jammed, leading to late or damaged goods for your customers, and massive bottlenecking and downtime issues for your logistics team.
That is why it is so important to invest in a solution that negates the chance for your packages to disrupt your workflow and cause issues. One such solution is Flexco’s Segmented Transfer Plates (STP).
The STP is designed to create a seal at your belted conveyor transfer points, allowing for a smooth transition from one belt to the next. Packages more easily and freely glide over, leaving essentially no opportunity for package jams within your conveyor system.
If you are currently operating your conveyor system without our Segmented Transfer Plates, you are at major risk for these issues, and more.
As I’m sure you can attest, every minute that your system is down equates to precious dollars lost. If those minutes turn into hours, and hours turn into days, the costs can be overwhelming.
If you are already using the Flexco STP technology – installing them is not where it ends; you must proactively maintain, refresh, and replace worn segments as needed.
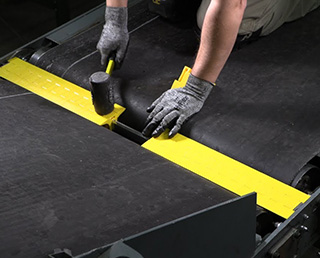
During my time at Flexco, I think the STP may be the most innovative yet simple piece of technology that I have worked with. It is as close as it gets to set-it-and-forget-it in the conveyor solutions world, but that does not mean neglecting it. The Flexco STP will provide you with years of loyal service with minimal upkeep.
My word of advice: set up a system in your facility for periodically checking your STP’s on a basis that makes sense with your product flow and output. Check for loose brackets, broken segments, broken bolts, and any other serious signs of wear. Then repair or replace worn units as needed.
The investment is small compared to the ROI gained!
View Application Profile
Fasten Those Belts
When your conveyors are not operating properly, problems can occur. Whether you’re dealing with belt slippage, tracking issues, or general damage and wear, simply taking a deeper look at your system, diagnosing the issue, and coming up with a solution is only half the battle; you have to proactively tune-up key areas of your conveyor system to better neutralize them.
Generally speaking, the best ways to combat most complications you may face are properly installed mechanical belt fasteners or endless splice. Improper installation is a key factor in splice failure, no matter which method you use for splicing your belts.
If you’re pressed for time and need the belt moving ASAP, in most applications, utilizing our tried-and-true mechanical belt fasteners is an excellent choice. But, for extremely critical applications, an endless splice might be the way to go. If you’d like to figure out which is best for you, contacting a Flexco expert.
Overall, it’s incredibly important to keep track of the performance of your belt at its connection point. If you have not been, it may be time for a tune-up.
Let’s Roll
At Flexco, our number one priority is safety. I would be willing to guess that your company holds a similar sentiment. Unfortunately, if you’re operating an intricate power-driven roller conveyor system, you know just how easy it can be for a worker to be put in a potentially dangerous situation.
An Answer to Transfers
The design of the roller conveyor makes packages, envelopes, and polybags susceptible to falling into the spaces in between rollers. In turn, workers have to retrieve mishandled packages, putting them at risk of sustaining an injury.
To lessen these risks, I advise you to look into Flexco’s Roller Conveyor Transfer Plates (RCTP). Once installed, product loss and worker interaction directly with the conveyor become a thing of the past.
Due to the snap-in place design of RCTPs, the installation process could not be easier. Simply do a pre-inspection of the cleanliness of your system and snap them into place. This process also makes them easy to repair if one of them becomes damaged.
View Application Profile
Pressed for Time
When a belt goes down from damage and wear in the middle of your operation, chaos ensues. Product can’t move; therefore, you can’t make money. And, depending on your industry, every day you’re not in full operation could cost you millions.
So, when your endless spliced belt needs repair or replacement, where do you turn? If it’s not Flexco, allow me to point out why it should be!
The Flexco line of Novitool® Aero® Splice Presses take your individual conveyor belt specifications into account, which is why we offer multiple lengths. If you have multiple belt types in your conveyor system, no worries, each Novitool® Aero® Splice Press has onboard splice recipe storage. Allowing quick retrieval of the recipe you need for that belt, at that time.
Why wait for an outside splicing crew? Purchase a Novitool® Aero® Splice Press in the length required for your system to give you ultimate control over splicing belts when it works for you. And, you will have peace of mind knowing that you have the necessary knowledge, and equipment on hand, to address any emergency splicing needs that may arise.
Designed with user-friendliness in mind, our Endless Convery Belt Splicing Tools are exceptionally convenient, both to use and to store, making it the ideal choice to bring in-house to your facility.
Once adopted, you will find that, when needed, the resolution time of an out-of-commission belt is drastically reduced. For example, an American retail distributor was regularly dealing with splice times of 60 minutes. But, when they utilized the Novitool® Aero® 325, they cut that time to 20 minutes, resulting in $36,666 in downtime savings per unscheduled belt splicing event.
View Application Profile
Ready for Repair?
In my opinion, the best way to see how much of an impact Flexco technology can have on your system is to actually try it. Flexco can make this happen. Whether you want to meet with us in-person at your facility or virtually, the team at Flexco will help you identify a solution that fits your specific needs.
It’s not too late to get back onto the road to higher productivity — schedule your demo today!
Schedule Demo
Authored by: Todd Stewart, Industry Manager
Stewart focuses on both the logistics industry, creating programs to support each segment and identifying customer issues, as well as potential product solutions, for parcel, airports, warehousing, distribution, and fulfillment. Stewart began his career at Flexco in 1989, working in various roles from customer service, to manufacturing, to training, to new product development, to market development management before taking on the role of Industry Manager in 2017. He earned a bachelor’s degree in Marketing with a B2B specialty from Davenport University.