Cuando está en el trabajo, día tras día, los problemas comunes del transportador de banda pueden pasar desapercibidos porque no los está buscando activamente. Pero una inspección visual rápida puede hacer la diferencia entre un día productivo y un día costoso para su operación agregada.
A continuación se incluyen los 10 desafíos principales de los transportadores que puede identificar con una simple inspección visual, qué problemas pueden causar y cómo solucionarlos en un corto período de tiempo.
Busque: daños en los limpiadores de la banda, desgaste prematuro de las grapas, material que se regresa pegado a la banda, desalineamiento de la banda.
Causas: Empalmes no desbastados, grapas que interfieren con los limpiadores.
Solución: desbaste la banda antes de aplicar los empalmes, cuando sea posible, y use grapas de bajo perfil con borde acuñado. Asegúrese de seguir todas las instrucciones del fabricante al empalmar, incluyendo colocar la banda en ángulo recto de forma correcta.
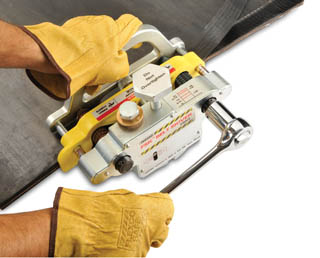
Si nota que sus grapas se desgastan prematuramente, desbastar la banda puede ser la clave para que el empalme tenga una vida útil más larga.
Busque: falla prematura en el empalme de banda, desgaste del recubrimiento irregular, desgaste prematuro de la cubierta en el canal.
Causas: poca distancia de transición.
Solución: revise las distancias de transición. Verifique que las distancias de transición estén en línea con los estándares de CEMA. Para las bandas de tela, CEMA generalmente recomienda una distancia de transición de 4.0 x el ancho de la banda.
Busque: desgarre de la banda justo detrás del empalme, falla prematura de la banda.
Causas: las grapas son demasiado grandes para la polea que es la más pequeña.
Solución: verifique si los diámetros mínimos de la polea (donde la banda se enrolla a 90 grados o más) están de acuerdo con las recomendaciones del fabricante de la banda y las recomendaciones del fabricante de la grapa. El uso de un diámetro de polea más pequeño que la banda o el tamaño recomendado de la grapa pueden producir tensiones de flexión excesivas con la posibilidad de que falle el empalme de banda.
Busque: resbalamiento de la banda.
Causa: poleas pequeñas.
Solución: el diámetro adecuado de la polea es esencial para el rendimiento de la banda. Cuando se trata del resbalamiento, el área de la superficie donde la banda pasa de la tensión total (superior) a la parcial (inferior) y se “encoge”, ejerce una gran presión sobre el recubrimiento para moverse con ella y evitar el resbalamiento. Si bien CEMA no recomienda específicamente un diámetro de polea por aplicación, los ingenieros de sistemas transportadores hacen recomendaciones para los diámetros de polea con base en el diseño del transportador. A menudo, la polea pequeña se sustituirá para ahorrar costos sin tener en cuenta este encogimiento de la banda: si minimizan el tamaño de la polea, también minimizan el área en la que el recubrimiento puede ayudar a encoger la banda cuando se enrolla alrededor de la polea. Reducir tanto el tamaño de la polea puede provocar resbalamiento.
Busque: desalineamiento, vida útil del empalme reducida.
Causa: la banda no está en ángulo recto.
Solución: coloque la banda a escuadra utilizando las herramientas adecuadas. Colocar la banda a escuadra implica marcar el centro de la banda en intervalos de 3 a 5 pies en aproximadamente 20 pies desde el área del empalme, dibujar una línea central con base en esas marcas y usar una escuadra para dibujar una línea perpendicular hasta la línea central promedio a través del ancho de la banda. No olvide usar una cortadora de banda adecuada (a diferencia de una cuchilla todo uso) para hacer un corte más recto y más seguro.
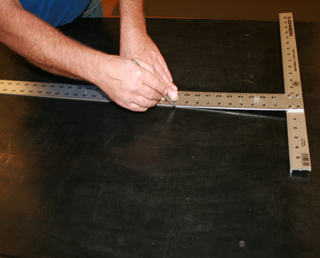
Algunas veces se pueden evitar las reparaciones rápidas. Una banda que está debidamente colocada a escuadra puede prolongar su vida útil y ayudar a evitar el desalineamiento.
Busque: derrames en la zona de carga.
Causa: faldones deficientes, sin protección contra impactos.
Solución: revise y de mantenimiento al faldón con un sistema fácil de usar. El faldón es importante en la zona de carga porque detiene los derrames de material, controla las emisiones de polvo y elimina otros problemas derivados, tales como daños en la banda y desalineamiento. Busque un sistema de faldón que sea fácil de reparar y que tenga componentes resistentes a la corrosión que requiera menos mantenimiento. También deseará asegurarse de tener la protección adecuada contra impactos y que la banda se apoye correctamente en el área de carga. La protección contra impactos debe tener en cuenta el peso en masa y la altura de caída, y debe brindar la máxima protección a su banda en la zona de carga.
Busque: daño en la banda, daño estructural del transportador.
Causa: desalineamiento de la banda.
Solución: identifique la causa del desalineamiento e instale un alineador de banda. La desalineación de los rodillos o poleas, un empalme incorrecto y acumulación de material son algunas de las cosas que pueden desviar su banda. Se ha comprobado que la fricción y la tensión proporcionan una alineación efectiva cuando se utilizan juntas. Elija un alineador con un diseño de pivote e inclinación que proporciona fricción y cambia el perfil de tensión de la banda.
Busque: daño en la banda porque los rodillos están atascados.
Causa: los rodillos atascados cortaron la banda.
Solución: inspeccione regularmente el transportador para ver si los rodillos están atascados (no giran). Para los rodillos de acero, busque puntos planos con bordes afilados; estos se deben reemplazar de inmediato o corren el riesgo de cortar la banda. Para los rodillos compuestos con núcleo de acero, busque puntos planos con bordes afilados; estos se deben reemplazar de inmediato o corren el riesgo de cortar la banda. Para los rodillos compuestos sin núcleo de acero, reemplácelos cuando sea posible.
Busque: los limpiadores de banda que no funcionen correctamente.
Causa: los limpiadores están instalados incorrectamente o la banda se curvó al pasar por los limpiadores.
Solución: asegúrese de que los limpiadores estén instalados correctamente al revisar las instrucciones de instalación. Si la banda está curvada, introduzca un rodillo estabilizador para nivelar la banda y garantizar que el contacto entre el limpiador y la banda sea correcto.
Busque: borde de limpieza deficiente y banda sucia.
Causas: ángulo de ataque deficiente, hoja desgastada u hoja incorrecta en referencia al trayecto del material.
Solución: la ubicación del eje es vital para el éxito del limpiador porque permite el ángulo de ataque correcto de la hoja, fomenta el máximo rendimiento de limpieza y asegura la máxima vida útil de la hoja porque se puede usar toda el área de desgaste de la hoja. Se puede lograr una limpieza óptima prestando mucha atención al trayecto del material de la banda, que suele ser el centro 2/3 del ancho de la banda. La elección de una hoja que es solo un poco más ancha que el trayecto del material puede disminuir el desgaste y el reemplazo de la hoja.
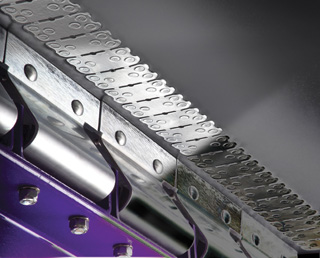
Asegurarse de que los componentes del transportador de banda son compatibles entre sí es clave para que todas las piezas funcionen sin problemas.
Junto con las revisiones visuales diarias, operaciones debe realizar una auditoría anual del transportador de la banda. Un equipo interno puede realizar la auditoría, pero la participación de un tercero es útil. Su equipo puede identificar y abordar las tareas de mantenimiento simples que pueden haber pasado desapercibidas, o se pueden reemplazar los componentes que harán que su equipo funcione de manera más eficiente. Si no hay nada más, una auditoría puede ayudar a mantener su equipo funcionando por más tiempo.
Con el tiempo, el material que se regresa pegado a la banda, el derrame, la selección incorrecta de las grapas y el desalineamiento pueden causar serios problemas en su sistema transportador de banda. Aunque estos pueden parecer problemas cotidianos, las soluciones están disponibles y son parte integral del éxito de su operación. Con demasiada frecuencia, los operadores de la planta ni siquiera se dan cuenta de que existe un problema hasta que se detiene la producción. Al final, todo afecta el resultado final de la operación. No deje que eso le pase a su operación.
Preparado por: Ryan Grevenstuk, Director de Mercadeo – Trabajo pesado
Grevenstuk es responsable de los planes comerciales y de mercado globales estratégicos, investigación de la industria y el mercado, el desarrollo de nuevos productos, la administración de relaciones con los clientes y el soporte técnico para las líneas de productos para trabajos pesados en Flexco. Tiene una licenciatura de Central Michigan University, así como una maestría de Western Michigan University.