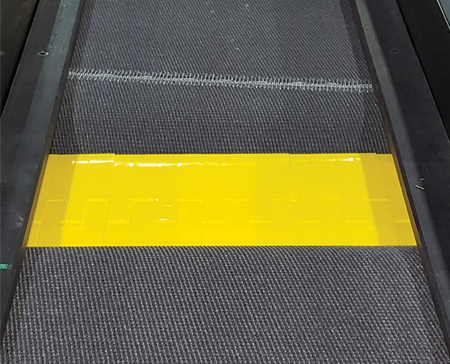
Industry
Warehousing and Distribution
Application
Horizontal to horizontal conveyor
Product
Segmented Transfer Plates
Objective
Reduce product jams
Minimize safety hazards
Reduce maintenance time
Conveyor Detail
Rubber belt transferring to modular belt
Problem:
The modular conveyors located at the distribution center of a major clothing retailer transport trays over pop out rollers to a conveyor bed to keep the line moving. Those pop out rollers suffered from premature wear because of the repeated contact with the tray, and they needed to be replaced regularly, costing the facility approximately $500 in parts and at least 80 hours in labor a year. In some cases, the rollers would fail and pop out, causing product jams at the transfer. This not only slowed the flow of product, but presented a safety hazard if an employee was compelled to stick their hand into the jam to clear it. On top of that, the retailer had to rework the clothes that fell to the ground or sell them at a loss.
Solution:
The operations manager knew that the problem was costing them time and affecting the quality of their product. So, the next time a Flexco Territory Manager was visiting the warehouse, they offered a solution – Flexco Segmented Transfer Plates. The Segmented Transfer Plates were the perfect solution because they covered the gap and created a tight seal to the belt, preventing product jams and increasing safety by minimizing potential crush points around the transfer.
Result:
Upon installing the Segmented Transfer Plates, the need for regular roller maintenance was eliminated and product flow is at peak system efficiency. Because jams at the transfer points were no more, the retailer no longer reports losses due to rework. The operation also saved approximately $500/year in parts used to replace the rollers and close to $10,000/year in labor. Safety was significantly improved with a reduction in crush points and pinch hazards at the transfer since the gap is being guarded by the visible yellow segments.