Let’s start with the fundamentals … what is carryback?
Carryback is the product that makes its way past the drop off point and runs back along the underside of the conveyor belt. The amount of carryback on the belt can depend on a number of factors including the type of product, whether it be iron ore, coal, or aggregate; the way the belt is oriented; or even the climate or environment surrounding the application. No matter what the cause, the goal is always consistent - to recover the carryback product before it creates hazards and results in a loss of productivity.
When carryback leaves the belt, it has to go somewhere; that somewhere is typically the ground, creating mountains of product. This isn’t only a significant on-site hazard, but it creates a clean-up job that can lead to unscheduled downtime for the site.
Carryback on a conveyor is inevitable no matter what the product, however avoiding this is typically no problem if you’ve got the right equipment installed. With some sites losing close to a ton of product every day just because of carryback, recovering the lost product seems like the obvious solution to an increase in productivity and revenue. However, picking the right equipment to solve the issue of carryback isn’t always as straight forward as a “one product fits all” type of purchase. Below we’ve outlined the best methods for combatting carryback.
The First Step: Selecting a Belt Cleaner
Picking equipment to combat carryback can vary depending on the application. While some options are more financially viable, they may not achieve the desired result in heavy-duty settings. Belt cleaning tools include precleaners, secondary cleaners, spray bars, and wash boxes. Each of these work effectively for different purposes; however on their own they don’t always eliminate carryback as a whole and can leave a gap in your defense.
Precleaners and Secondary Belt Cleaners
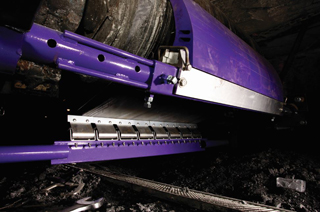 |
Flexco Precleaner and Secondary Cleaner |
Precleaners (also called belt scrapers) with tungsten carbide tips or polyurethane blades are designed to scrape material off the conveyer belt, and are usually positioned on the head pulley. Precleaners are designed to scrape off up to 60%-70% of material, typically removing the larger pieces. However, when the material is sticky, there is a humid climate, or there is simply not enough room precleaners need more help to clean the belt. In these circumstances, many will chose to employ a secondary or even a tertiary cleaner.
However, we can imagine you want to clean off more than 70 percent of your carryback ...
Secondary belt cleaners are belt cleaners that are built to scrape materials left on the belt beyond the head pulley. Secondary cleaners are located just beyond where the belt leaves the head pulley, and anywhere else where necessary down the beltline. Secondary cleaners are especially good at removing fines and can, in some settings, increase cleaning efficiency to more than 90 percent. However, if you’re working with extremely sticky material or in abrasive or corrosive climates, you may need a heavier-duty solution.
Taking It up a Notch: Incorporating Water
Typically used alongside secondary cleaners, spray bars (also referred to as spray poles) offer another source of protection in combatting stubborn carryback. Adding water to the equation helps either break down or collect remaining carryback in a form that is easily cleaned from the belt.
Water can have drawbacks including: uncontrolled material movement, spillage, and material degradation. Issues like this can result in downtime and clean-up cost, equipment damage, and corrosion of the conveyor structure and components.
However, a well thought out water management program can typically outweigh these negatives. Plans that incorporate a recycled water system and controlled runoff will negate these issues. Along with water management systems, investing in a spray bar that has a maximum inlet pressure of 145 PSI will give you the perfect balance between having enough water to clean your belt, and avoiding nasty issues like material degradation. Allowing your site to incorporate a water-based cleaning system is often integral to the productivity of a cleaner when a standard cleaning system just won’t do.
Finally, the Ultimate Cleaning System
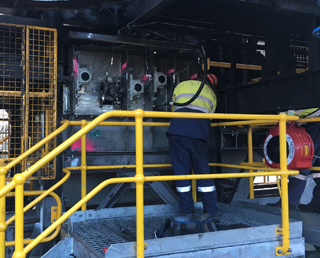 |
A wash box undergoing inspection. |
In some settings, a precleaner, secondary cleaner, or spray bar just don’t cut it when trying to remove carryback. Incorporating a wash box into your conveyor allows you to virtually eliminate carryback, even in the toughest applications.
A wash box is a fully enclosed system which incorporates both belt cleaners and spray bars. The spray bars flush material off the bottom pan out the drain portal, fully containing the waste wash water. This means you get a clean belt and waste water management system in one.
Make the Move
Ready to make the move towards clean belt by taking the steps outlined above, or are you still not sure where to start? Request a free assessment today and one of our Flexco experts will evaluate your entire belt conveyor system and help you find the right solutions for your challenges.
Authored by: Kevin Fales, Product Manager
Fales manages the belt conveyor product (BCP) line, providing product development and engineering with guidance on market requirements for both new product concepts and existing products. He also leads the development of technical and promotional literature supporting BCP line. Fales graduated from Grand Valley State University with a bachelor’s degree in Marketing, and from Western Michigan University with a Master of Business Administration.