Sanitation. Sanitation. Sanitation. It’s a word that is spoken on a repeated basis in industrial bakeries all over the world. Clothing and footwear protocols, hygiene protocols, conveyor belt cleaning protocols – they all include some mention of sanitation. Any chance we have to make our processes more sanitary, especially when dealing with raw materials, we should take.
And that includes your belt splices.
According to a recent article in Food Safety Magazine, we can’t count on the oven to kill all the microbial hazards on the food products or belt. Staphylococcus aureus and Bacillus cereus can lurk well beyond the cooking process.
Because of this, we need to make sure that the conveyor belt doesn’t give these menaces a place to live and thrive. One of the ways we do this is by installing endless splices – the most sanitary method for splicing.
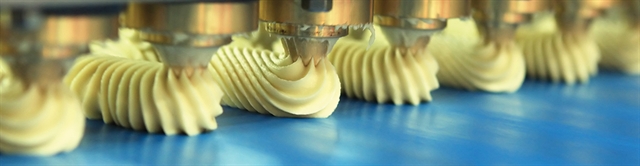
What do we mean by sanitary splices?
To obtain a sanitary splice, we want the conveying surface to be completely sealed to avoid bacteria growth or the transfer of food allergens from product to product. The last thing you want is gluten in some gluten-free bread, or even worse, some peanut dust making its way into a nut-free product.
Basically, you are looking to continue the natural surface of the belt, keeping it as uniform as possible. If you run your hand across the belt and feel dips and bumps, your belt might be carrying some extra passengers in the form of bacteria.
 |
Did you know? Another benefit of a smooth endless splice is better compatibility with belt cleaners. Proper blade-to-belt contact not only ensures a cleaner, more sanitary belt, but also reduces belt wear. |
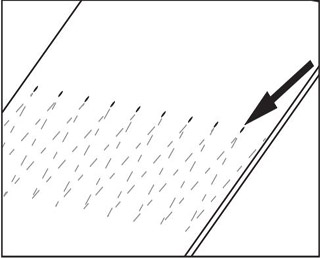 |
Pinholes generally occur near the tips of the fingers, where there tends to be more of a gap. |
What to look for in a splice
Aside from running your hand over the belt, there are other things you can look for when trying to figure out if your endless splice is properly sealed. Examine the splice to ensure that there are no “pinholes,” which are small indentations in the belt. Pinholes often occur near the tips of the fingers in the splice. When the thermoplastic in the PVC or PU do not flow into place properly, pinholes will often develop. If you are having problems with pinholes, we suggest checking out this article which details how to avoid them.
Proper bleedthrough is also one of the ways you can determine if your splice is done correctly. When you flip the belt over, you should be able to see the finger pattern bleed through the bottom of the belt like the photo below, but there shouldn’t be an obvious indent between the fingers on the top side of the belt.
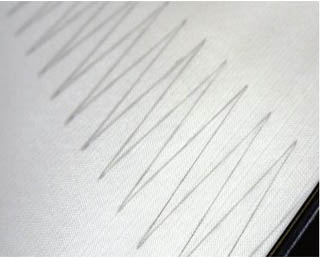
Water-cooled vs. air-cooled press
This brings us to the water-cooled vs. air-cooled press debate. They both have benefits, but which is better for a sanitary splice?
Some of the most recent advancements in endless splicing involves utilizing a cool zone around the perimeter of the splice. The transition from the heat zone to the cool zone eliminates ridges on either side of the splice by not allowing displacement of molten thermoplastic moving outward. This results in an entirely flat surface area.
Finally, the external water tanks and controls on water-cooled presses are not conducive to a sanitary environment. Bacteria and toxins could be hiding in the water, buckets, or tanks that are used in the splicing process. With air-cooled presses, those external components are not an issue since everything is self-contained in the press.
The best way to ensure sanitary splices
Bringing your equipment in house is one of the best ways to ensure sanitary splices in your bakery. The Novitool® Aero® Splice Press produces fast, sanitary splices thanks to its lightweight design and revolutionary cool zones. Keeping it onsite will also allow you to put your press through your own sanitation protocol instead of hoping that your outside contactor did their due diligence after their last repair. That contractor can still come in and splice your belts, but with your sanitized equipment, giving you confidence that you’re doing everything you can to keep your plant free from outside contaminants.
Authored by: Michelle Graves, Product Manager
Graves manages the overall global business, market plans, technical support, and activities associated with the light-duty belting market for the Novitool® product line, including new product development, market analysis, and global strategy. Graves holds a bachelor’s degree from Albion College as well as a master’s degree from Grand Valley State University.