Developing a new splice recipe for an endless conveyor belt can be a challenging process – especially when there’s insufficient technical information available. Experienced belt fabricators know that a recipe for a given belt will often work on one type of splice press, but not another.
Given that Flexco has a ton of endless splicing knowledge within its global team, we felt that splice press recipe development would be the perfect topic to address in a blog. But we knew one blog would not be enough to get the basics done, so we created two – Part I and Part II.
In last week’s blog, we focused on where to begin when creating a recipe, with a special focus on how belt type affects your recipe. In this blog, we will focus on the fundamentals of belt splice recipe development, as well as other tools and techniques that will help you determine the correct belt.
Fundamentals in Splice Recipe Development
Once you have your belt type identified, you’ll want to consider the three other important ingredients in your recipe: temperature, pressure, and time.
- Temperature: Consider the ideal splicing temperature. It needs to be high enough for the plastic to flow, but be careful to not program temperatures too high, as this will degrade the polymer chains and significantly weaken the mechanical properties of the belt. How do you know this happened? The splice will exhibit brown spots on the cover and/or bottom. Those brown spots are signs that premature splice failure and downtime are in your future.
- Pressure: Determine the right amount of pressure to move the plastic. There needs to be enough pressure to move the plastic to consistently fill the gap between the fingers, but not too much that will force the plastic to excessively flow through the fingers resulting in bleed through, or worse, fingers washing out. The ideal amount is a thin, solid line at the edges of the fingers. Excessive bleed through will change the coefficient of friction between the belt and conveyor components.
- Time: This movement doesn’t happen instantaneously, so a certain amount of time is needed for this material movement to occur.
All of these things are interrelated, which complicates the splice recipe development process. For example, if there is not enough temperature, PVC will flow at a slower rate. In this case, increasing pressure and/or dwell time may result in an acceptable splice, but increases bleed through. A preferred alternative might be to increase the temperature instead, allowing the plastic modules to flow easier.
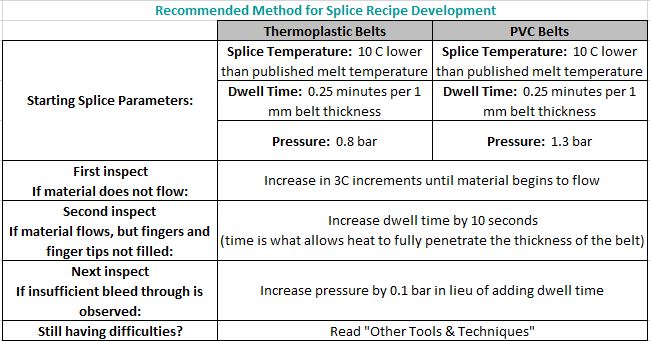
Other Tools and Techniques
Even if you have all your ingredients in place, there are a few more variables that can affect your splice, including preheating, top and bottom press temperature variations, and the use of foil.
Preheating: Because of the speed of quick cycle presses, there can be instances when it is necessary to slow the heat ramp up to allow heat to penetrate fully through the belt thickness and obtain a proper splice. If a belt is on the thicker side or is a profiled belt with a reverse patterned silicone pad, it may require the use of “preheat” to properly soak heat throughout the entire belt thickness prior to splicing.
In a way it is similar to cooking frozen meat. Without allowing it to defrost prior to placing it in a hot oven, you will likely find the outside of your meat cooked properly but the inside still raw.
When splicing thick belts, or when thick profile pads are used, use a press that can be programmed for a lower temperature and held at this point for a number of minutes to allow the full belt thickness temperature to rise close to the final splice temperature. This is called the preheat cycle. Once the preheat cycle is complete, the press can increase its temperature to meet the splicing temperature and complete the cycle, resulting in proper and consistent bleed through for a strong, finished splice.
Top and Bottom Press Temperature Variations: Belts are typically not symmetrical in their composition and there are instances different temperatures should be applied to the top and bottom platens. An example would be a belt where bleed through is evident on the bottom, but the fingers aren’t filled. In this instance, consider decreasing the bottom splice temperature and increasing the top splice temperature.
Another example would be higher durometer PVC formulations (e.g. diamond profile at the bottom of the belt), which do not flow as easily. They might need an extra 5-10 degrees C (41-50 degrees F). The reverse might be true for very soft formulations.
Choosing a press that allows users to program different temperatures for top and bottom platens is key. Flexco’s Novitool® Aero® Splice Press allows you to do that in these special circumstances.
to request a demo of the Aero Press.
The Use of Foil: Typically, the use of foils is not necessary when finger splicing if proper time and attention are given to creating optimal splice parameters. Splicing without foils is preferred, as the foil adds thickness variation and does not provide additional strength. That being said, there are still belts with extremely thin top covers and there are instances when it is necessary to fill in pinholes at the fingertips.
Most belt manufacturers sell foil in coils, but another option to consider is using a ply separator to make your own foil from the base belt material (a great use for remnants). Flexco’s Novitool® Ply 130™ Ply Separator is just the tool for this job, precisely separating thermoplastic belts as little as 0.014” (0.35mm) to create foil.
Practice Makes Perfect With Splice Recipe Development
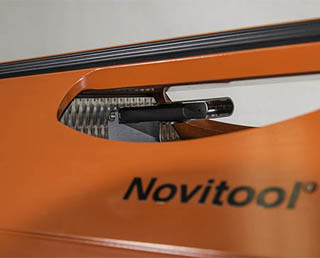 |
With the Aero® Press, recipes can then be exported from the tool and transferred to your press via a USB flash drive. |
Although some scientific principles can be applied to setting splice parameters, remember that it is an art, not a science. It will take a bit of trial and error, but operators should be able to begin with a good starting point and then methodically work to produce the optimal splice. Remember temperature, time, and pressure can always be added, but never taken away. The good news is that once the splice parameters are created, you can document them for future use. The Aero Press even has a recipe management tool that allows you to store more than 1,000 recipes between tools and across locations.
Authored by: Michelle Graves, Product Manager
Graves manages the overall global business, market plans, technical support, and activities associated with the light-duty belting market for the Novitool® product line, including new product development, market analysis, and global strategy. Graves holds a bachelor’s degree from Albion College as well as a master’s degree from Grand Valley State University.